Usina produz asfalto para a Cidade há 45 anos
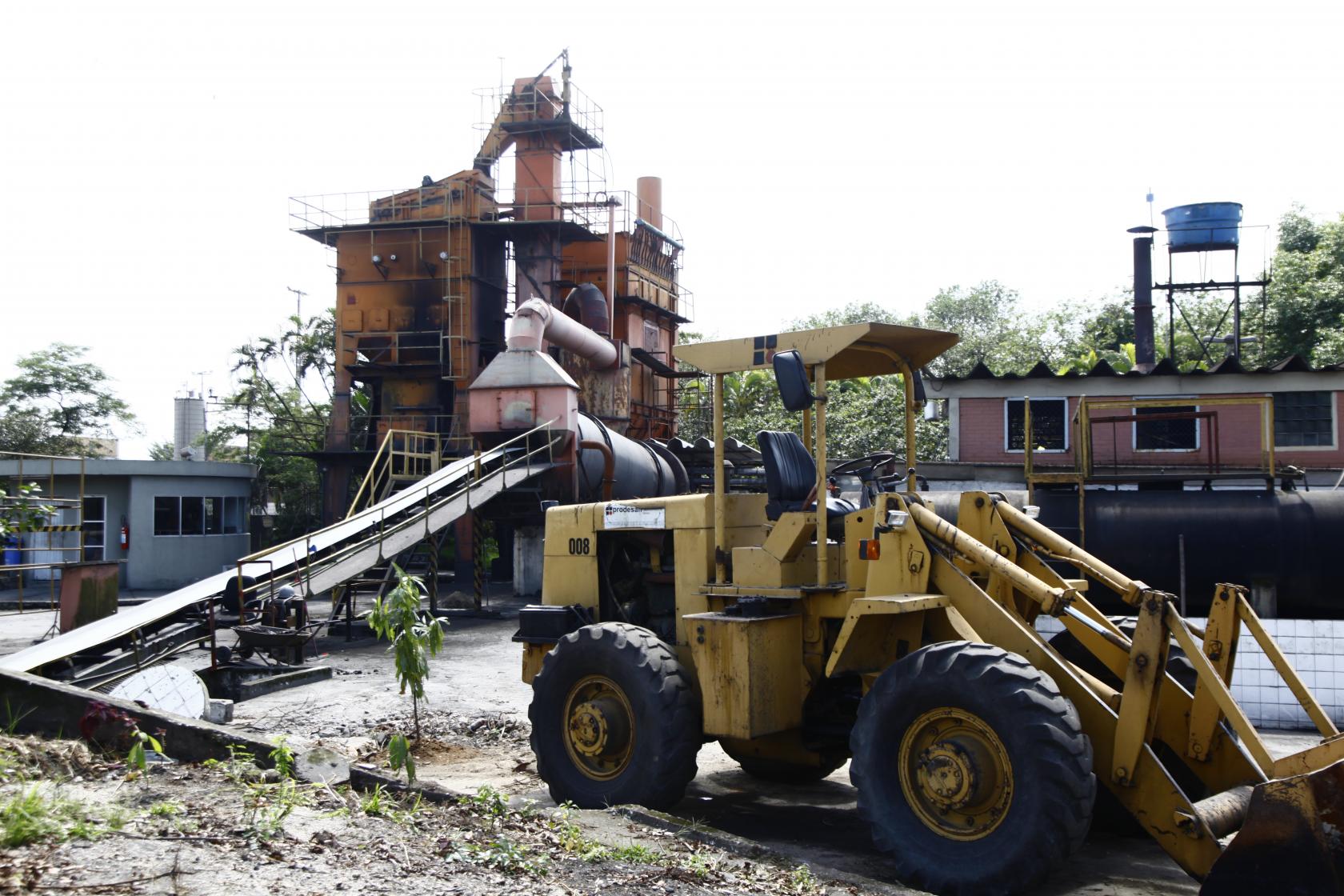
Todos os veículos trafegam sobre ele, mas poucas pessoas conhecem o seu processo de produção e sua função na via. É o pavimento asfáltico, que em Santos sai de um único lugar: a Usina de Asfalto da Prodesan. Com 75 funcionários e em funcionamento em uma área de aproximadamente 30 mil m², na Av. Vereador Alfredo das Neves (Alemoa), a unidade registra desde seu início, há 45 anos, até novembro último, a produção de 2.167.849,43 milhões de toneladas de asfalto.
Vendido à Prefeitura e empresas de médio e grande porte, o volume do material daria para asfaltar algo em torno de 1.806 quilômetros de ruas, cada uma com 10 metros de largura, ou mais de quatro vezes os 418 quilômetros da parte insular da Cidade, excluindo os morros.
A receita do ‘bolo’ de asfalto, como o gerente da usina, Rômulo Barroso Villaverde, gosta de chamar o processo de produção, compreende dois ingredientes: cimento asfáltico de petróleo (CAP) e pedras de três tamanhos (pó de pedra, pedrisco e pedras um pouco maiores). Entre as variedades de produção, a aplicada na pavimentação das vias da Cidade e das estradas é chamada na usina de ‘faixa 3’; em outras palavras uma massa asfáltica mais densa e de melhor compactação.
Geralmente, a espessura dela é de 5 cm nas pistas de rolamento e, embora possa parecer fina para suportar o peso de veículos, especialmente os mais pesados, é considerada suficiente, uma vez que a base do pavimento, feita de pedras, é o fator determinante para medir a capacidade de peso suportável, segundo o gerente Villaverde.
Quando não possui 5 cm, a espessura da camada asfáltica pode chegar a 10 e até 15 cm, como é o caso da Via C, no Alemoa, devido ao intenso tráfego de veículos pesados. “Uma base bem executada garante a vida útil do pavimento, em torno de 15 anos. O asfalto é flexível e tem duas funções: proteger a base da infiltração de água e oferecer um bom rolamento para os automóveis”, explica Villaverde.
Composição começa no laboratório
É dentro de um laboratório de controle de qualidade, instalado dentro da usina, que nasce a ‘receita do bolo’ da massa asfáltica solicitada pelo cliente. Os laboratoristas fazem o projeto com as porcentagens de cada material, usando balanças, peneiras para as pedras, entre outros equipamentos de precisão.
O trabalho desta equipe continua com os testes do que foi produzido, como a resistência da massa quando colocada em uma prensa. Somente após essa e outras avaliações, começa a produção do material encomendado.
ALTAS TEMPERATURAS
Atrás do prédio com as salas administrativas, laboratório de controle e de uma grande área verde, está a usina; para entender o passo a passo, o trabalho inicia com a coleta das pedras, que podem ser vistas em grandes montes a céu aberto, numa área chamada de estoque do material agregado.
Dali são recolhidas e transportadas por uma espécie de esteira que as leva até um supersecador, para tirar toda a umidade do material em uma temperatura de 900°C, etapa fundamental para o asfalto ser produzido. “Depois, as pedras são levadas ao alto da torre da usina, onde há um conjunto de peneiras que as separa novamente para serem misturadas nas porcentagens estipuladas no laboratório com o concreto asfáltico de petróleo”.
Em uma temperatura de 160°C, a massa asfáltica é injetada dentro do caminhão basculante e coberta com uma lona para não perder a temperatura nem endurecer. A partir daí, o trabalho segue para as ruas via serviços de pavimentação ou tapa-buraco. Em Santos, por ser uma cidade quente, o material pode circular pelas ruas no caminhão por até 6h. “Se a temperatura baixar para uns 140°C, a compactação não será tão eficaz. Duas horas são suficientes para a secagem do produto sobre a base”, explica Rômulo.
Fotos: Rogério Bomfim